Video
TR60 Main Technical Specification
TR60 Rotary drilling rig | |||
Engine | Model | Cummins | |
Rated power | kw | 97 | |
Rated speed | r/min | 2200 | |
Rotary head | Max.output torque | kN´m | 60 |
Drilling speed | r/min | 0-80 | |
Max. drilling diameter | mm | 1000 | |
Max. drilling depth | m | 21 | |
Crowd cylinder system | Max. crowd force | Kn | 90 |
Max. extraction force | Kn | 90 | |
Max. stroke | mm | 2000 | |
Main winch | Max. pull force | Kn | 80 |
Max. pull speed | m/min | 80 | |
Wire rope diameter | mm | 18 | |
Auxiliary winch | Max. pull force | Kn | 40 |
Max. pull speed | m/min | 40 | |
Wire rope diameter | mm | 10 | |
Mast inclination Side/ forwards/ backwards | ° | ±4/5/90 | |
Interlocking Kelly bar | ɸ273*4*7 | ||
Undercarrige | Max. traveling speed | km/h | 1.6 |
Max. rotation speed | r/min | 3 | |
Chassis width | mm | 2600 | |
Tracks width | mm | 600 | |
Caterpillar grounding Length | mm | 3284 | |
Working Pressure of Hydraulic System | Mpa | 32 | |
Total weight with kelly bar | kg | 26000 | |
Dimension | Working (Lx Wx H) | mm | 6100x2600x12370 |
Transportation (Lx Wx H) | mm | 11130x2600x3450 |
Product Description
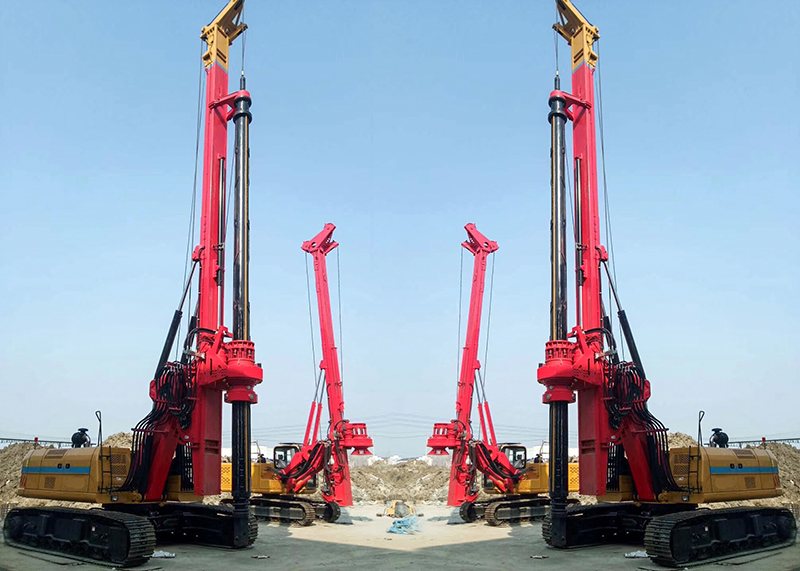
TR60 rotary drilling is new designed self-erecting rig, which adopts advanced hydraulic loading back technology, integrates advanced electronic control technology. The whole performance of TR60 rotary drilling rig has reached advanced world standards.
The corresponding improvement on both structure and control, which makes the structure more simple and compact the performance more reliable and operation more humanized.
It is suitable for the following application:
Drilling with telescopic friction or interlocking Kelly bar – standard supply.
Features and advantages of TR60
The rotary head has the function of spin off speed; the maximum rotation speed can reach to 80r/min. It completely solves the problem of soil off difficulty for small diameter pile hole construction.
The main and auxiliary winch are all located on the back of mast which are easy to observe the direction of the rope. It improves the mast stability and construction safety.
Cummins QSB3.9-C130-31 engine is chosen to meet the state III emission requirements with economic, efficient, environmentally friendly and stable characteristics.
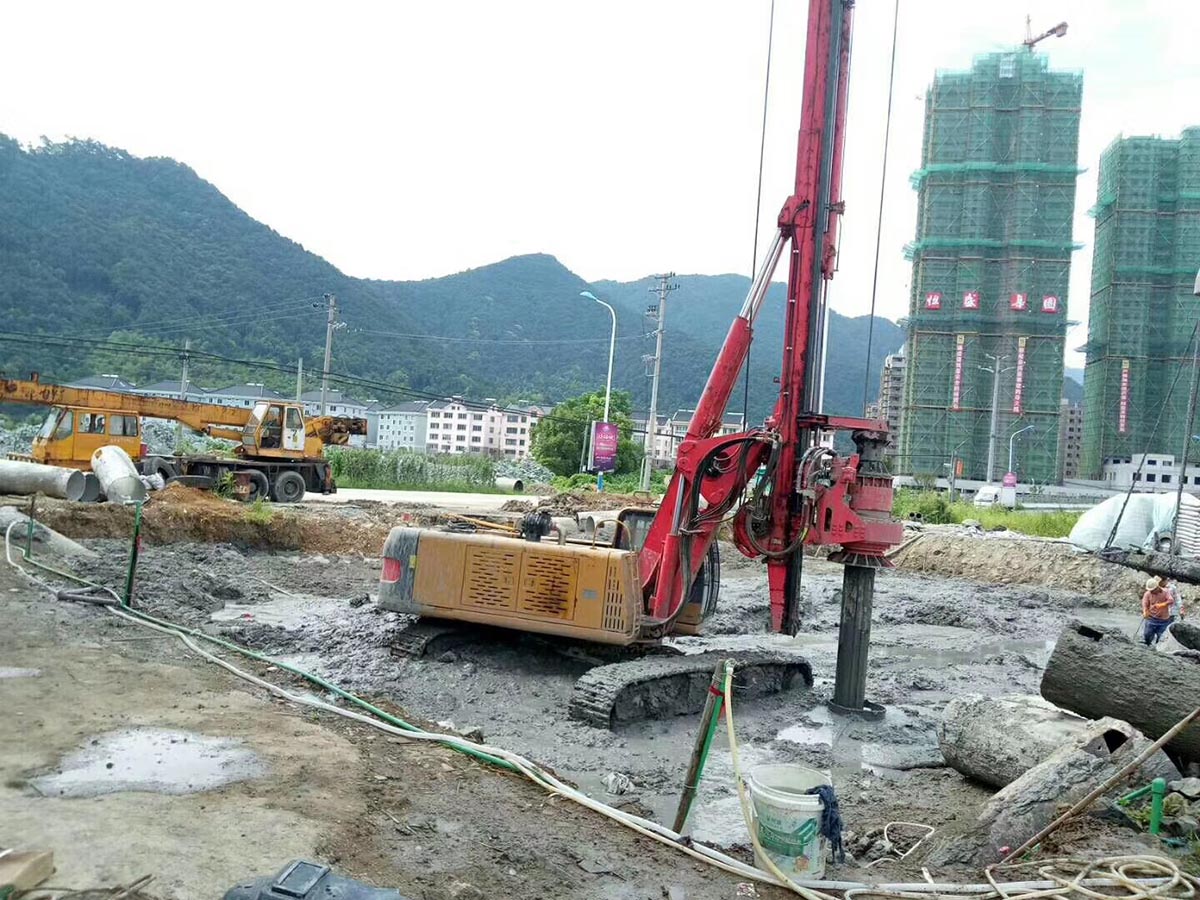
The hydraulic system adopts the international advanced concept, specially designed for the rotary drilling system. Main pump, rotary head motor, main valve, service valve, travelling system, rotary system and the joystick are all import brand. The auxiliary system adopts the load-sensitive technology to realize the on-demand distribution of the flow. Rexroth motor and balance valve are chosen for the main winch.
It is no need to disassemble the drill pipe before transporting. The whole machine can be transported together.
All the key parts of the electric control system (such as display, controller, and the inclination sensor) adopt international famous brands EPEC from Finland, and use aviation connectors to make special products for domestic projects.
Construction Cases
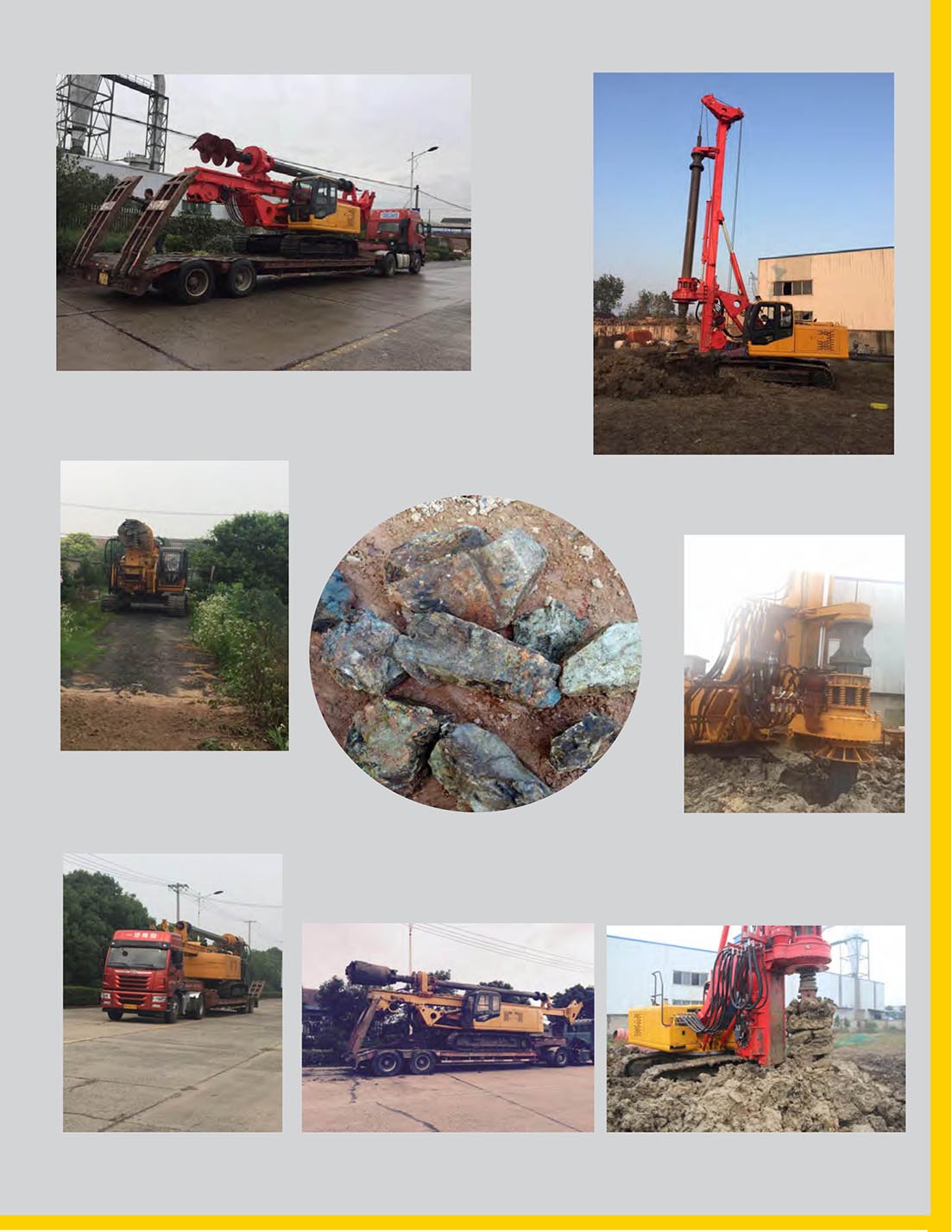