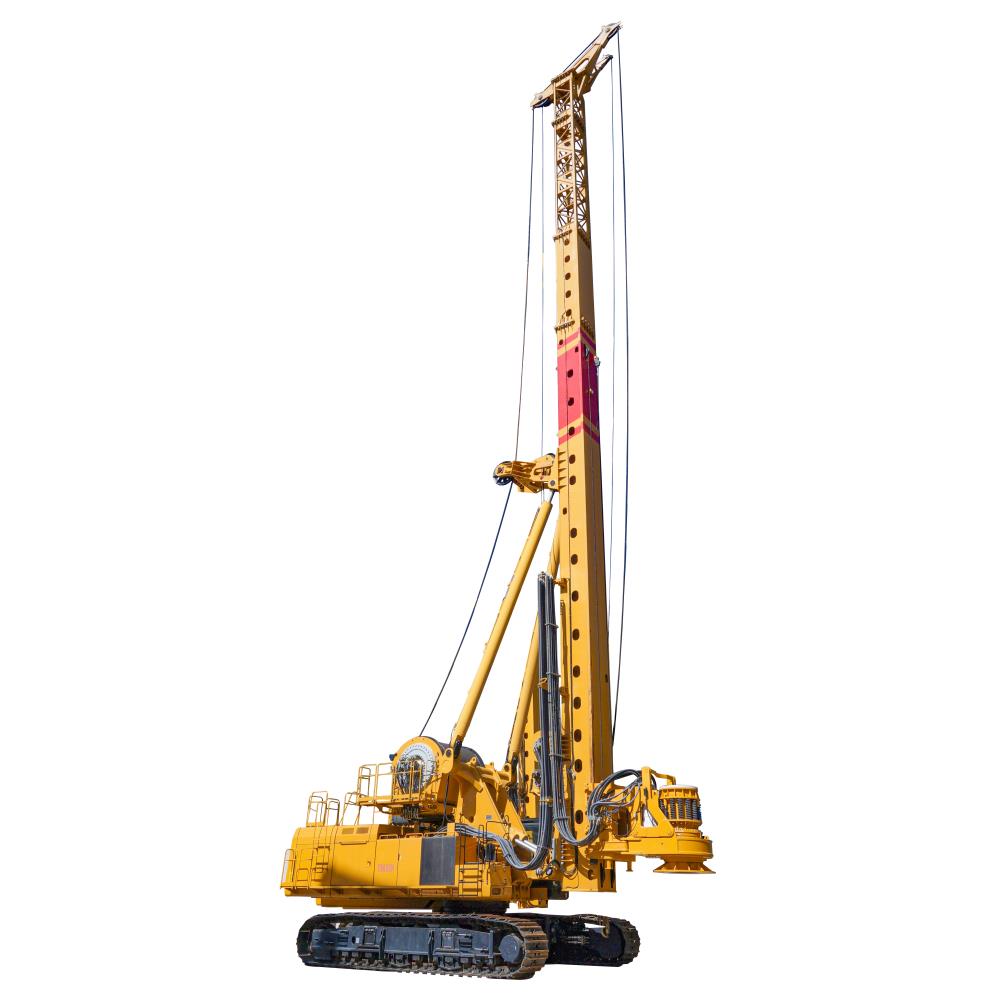
TR600H Rotary Drilling Rig is mainly used in the super large and deep construction of civil and bridge engineering. It obtained a number of national invention patents and utility model patents. Key components use Caterpillar and Rexroth products. The advanced intelligent electronic control system makes the hydraulic control more sensitive, accurate and fast. The advanced intelligent electronic control system makes the hydraulic control more sensitive, accurate and fast. The machine operation is safe and reliable, and a nice human-machine interface.
Main Parameters of TR600H Rotary Drilling Rig:
Pile |
Parameter |
Unit |
Max. drilling diameter |
4500 |
mm |
Max. drilling depth |
158 |
m |
Rotary drive |
||
Max. output torque |
600 |
kN·m |
Rotary speed |
6~18 |
rpm |
Crowd system |
||
Max. crowd force |
500 |
kN |
Max. pulling force |
500 |
kN |
Stroke of crowd system |
13000 |
mm |
Main winch |
||
Lifting force (the first layer) |
700 |
kN |
Wire-rope diameter |
50 |
mm |
Lifting speed |
38 |
m/min |
Auxiliary winch |
||
Lifting force (the first layer) |
120 |
kN |
Wire -rope diameter |
20 |
mm |
Mast inclination angle |
||
Left/right |
5 |
° |
Backward |
8 |
° |
Chassis |
||
Chassis model |
CAT390F |
|
Engine manufacturer |
CATERPILLAR |
|
Engine model |
C-18 |
|
Engine power |
406 |
kW |
Engine speed |
1700 |
rpm |
Chassis overall length |
8200 |
mm |
Track shoe width |
1000 |
mm |
Tractive force |
1025 |
kN |
Overall machine |
||
Working width |
6300 |
mm |
Working height |
37664 |
mm |
Transport length |
10342 |
mm |
Transport width |
3800 |
mm |
Transport height |
3700 |
mm |
Total weight (with kelly bar) |
230 |
t |
Total weight (without kelly bar) |
191 |
t |
Main Performance and Features of TR600H Rotary Drilling Rig:
1. It uses retractable caterpillar chassis. CAT counterweight is moved to the backwards and variable counterweight is added. It has nice appearance, comfortable to operate, energy saving, environmental protection, reliable and durable.
2. Germany Rexroth motor and Zollern reducer go well with each other. The core of hydraulic system is the load feedback technology which enables the flow to be allocated to each working device of the system according to needs to realize best matching under different working conditions. It saves engine power greatly and reduces energy consumption.
3. Adopt middle mounted main winch, crowd winch, box section steel plate welded lower mast, truss type upper mast, truss type cathead, variable counterweight (variable number of counterweight blocks) structure and axis turntable structure to reduce the weight of the machine and ensure overall reliability and structural safety.
4. The vehicle mounted distributed electrical control system integrates electrical components such as foreign vehicle mounted controllers, displays and sensors. It can realize many functions of engine starting and stopping monitoring, fault monitoring, drilling depth monitoring, vertical monitoring, electromagnetic reversing protection and drilling protection. The key structure is made of steel plate with fine grain of high strength up to 700-900MPa, with high strength, good rigidity and light weight. And carry on the optimized design combined with the result from finite element analysis, which makes the structure more reasonable and design more reliable. The use of advanced welding technology makes it possible for super large tonnage rig to be light weight.
5. The working devices are joint researched and designed by first-class brand manufacturers which ensures the best construction performance and construction efficiency. Drilling tools can be selected according to different working conditions so as to ensure smooth construction of the rotary drilling rig under different working conditions.